January 11, 2024
At Mizzou Engineering, we encourage students to constantly question reality to inspire them to engineer a better world. And we persistently provide hands-on learning opportunities for students. That’s why capstone courses are a key pillar of our curriculum as they allow students to apply concepts they’ve learned in their classes.
Students studying industrial engineering work with a client to develop a solution to an engineering problem. This fall, one capstone group was assigned to work with American Air Filter (AAF) to reconfigure their production layout for one of the company’s products. They documented their project and process, showcasing another example of how a Mizzou Engineering education prepares students for their careers.
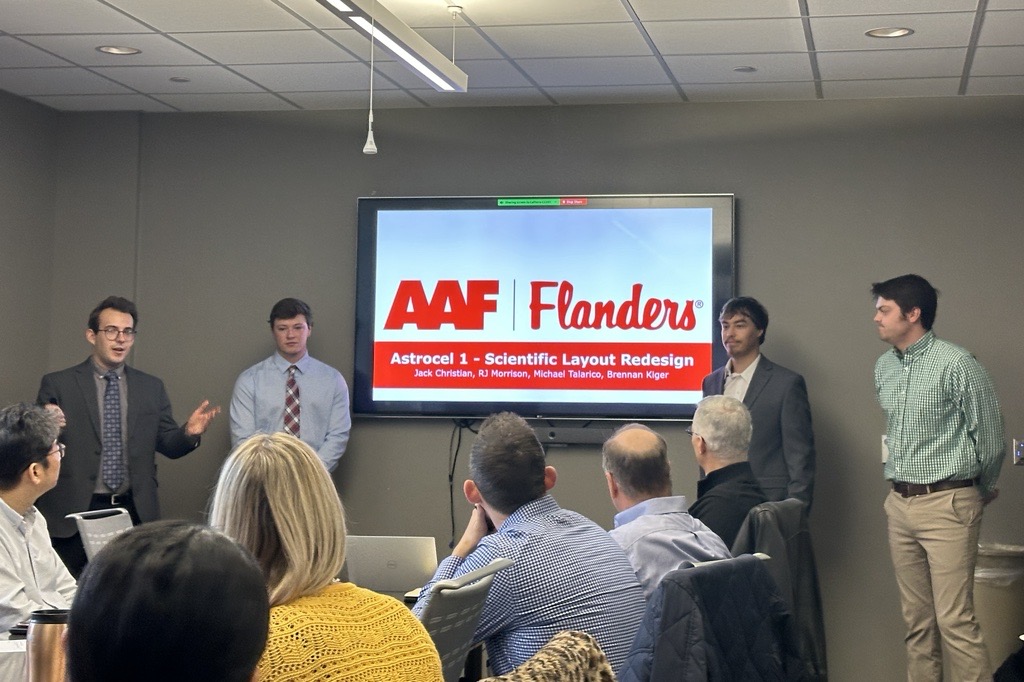
The Project
The capstone group’s work centered around two goals. First, AAF was getting new equipment to crimp bigger rolls of sheet metal, and the new machines would extend 21 feet further into the workspace than the current machines. Because of this, the capstone team used industrial engineering principles to reallocate other equipment and materials to provide space for the new crimpers, without negatively impacting the efficiency or safety of the workers.
While visiting the facility, the capstone group found that a significant amount of floor space was being used to hold pallets of raw materials. This brought a second objective for the capstone group—to develop a space-saving inventory management system.
The Process
To successfully complete the project, the team had to reallocate 735 square feet of equipment and workspace while maintaining safe walkways and ergonomic workspaces, maintaining or reducing travel distance per product and maintaining or improving production rates.
“To walk through the production process,” said RJ Morrison, “From the crimping machines, the material then goes to folders, which slowly push out folded and crimped filters toward a table for assembly before they move through the rest of the factory. Moving the crimpers will affect space up until the assembly tables.”
After coming up with proposed solutions, the team visited AAF in Columbia to perform a Kaizen test in which the company and workers took a day to implement new layouts for the workspace and share their feedback.
“A lot of the changes that were made involved getting rid of unnecessary equipment or moving equipment to spaces it fits better,” said Jack Christian.
The team solved the inventory management problem with a racking system.
“What we were trying to create with these racks is a new way to organize all the parts into these different spaces,” said Michael Talarico. “This will improve both the ergonomics of having to bend over into the box and pick up parts and also make locating the parts much easier than having them separated in boxes with different labels.”
During the Kaizen test, they also tested different sizes of racks for inventory to be stored based on what would be easiest for the workers to use and maneuver around while still holding 2-7 days’ worth of supplies.
The Outcome
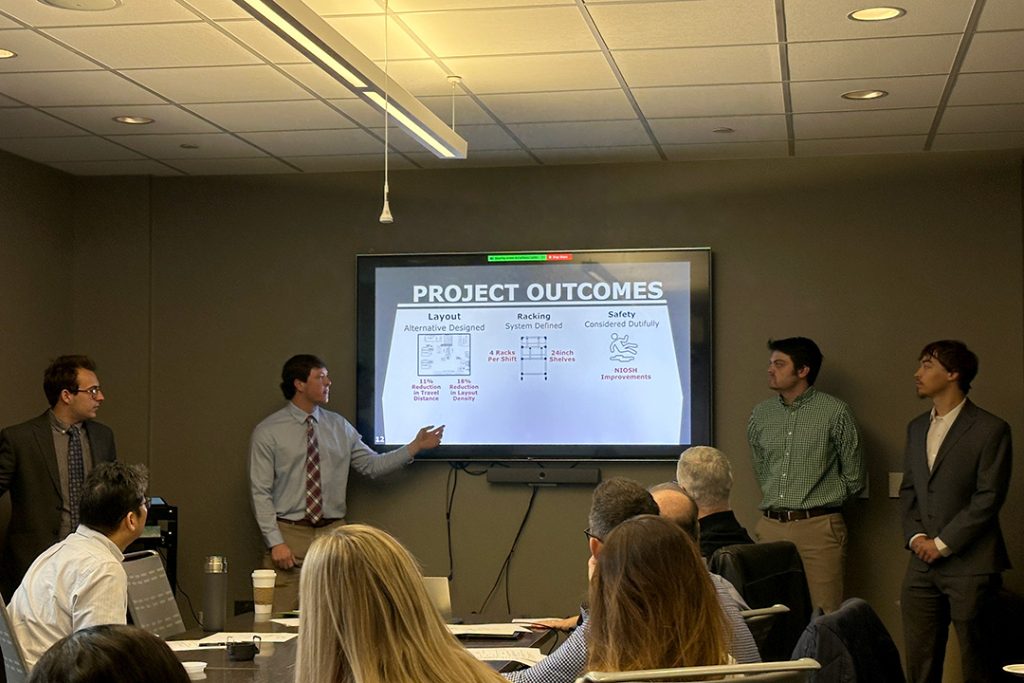
Based on the Kaizen test of the new layout and calculations by the team, their proposed layout solution included an 11% reduction in travel distance for the workers per product and an 18% reduction in layout density. The racking system was also deemed beneficial for production, with the team recommending four 24-inch shelves per work shift. And all the proposed changes led to a statistically safer work environment.
“We improved throughput by decreasing the material travel distance as well as decreasing safety risks by making various ergonomic improvements,” said Brennan Kiger. “We’re proud of the work we’ve done.”
Discover industrial engineering at Mizzou!