January 11, 2024
At Mizzou Engineering, we know that there’s no substitute for learning through experience. We persistently provide hands-on learning opportunities for students to find creative solutions to engineering problems. That’s why capstone courses are a key pillar of our curriculum as they allow students to apply concepts they’ve learned in their classes.
Students in mechanical engineering work with clients to solve a real-world problem, which can involve both coming up with a solution and developing a product. This fall, one capstone group documented their project and process to showcase another example of how a Mizzou Engineering education prepares students for their careers.
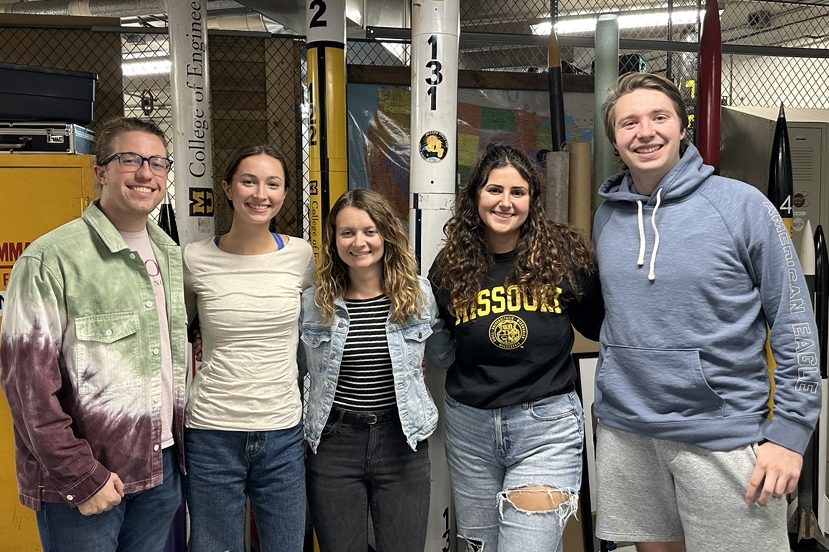
The Project
The group worked with their client, Mizzou Space Program, to develop an airbrake system to improve accuracy of rocket flight altitudes.
“Mizzou Space Program (MSP) competes in a few different high power rocketry competitions including the Spaceport America Cup,” said Abigail Penfield. “MSP recently competed in a 10,000 ft Student Researched and Designed Motor category, so that means we were aiming for a 10,000-foot apogee, or the highest altitude. Teams get a higher score if they get closer to that target apogee. Our capstone group is working on an air brake system as a proof of concept that MSP can innovate upon on and use for future competition rockets to get higher scores because they can reach closer altitudes to their target altitude.”
The project had ample opportunities for the group to learn skills valuable to the job market.
“We chose this project because we wanted something that we could focus on the design portion, the testing portion, manufacturing and then continue making iterations throughout that entire process,” said Willa Zwingle.
The Process
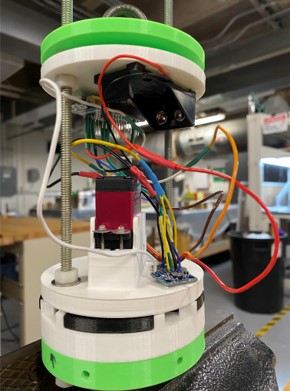
In flight, wind flows around the rocket, and after the air brakes deploy, they slow the rocket by creating drag. How much the air brakes would slow down a rocket depends on the rocket’s velocity. To find out exactly how much, they tested prototypes inside a rocket attached to the top of a car. They developed prototypes using the 3D printing lab in Lafferre Hall, a resource all capstone groups have access to.
“We drove around a park, safely, at different speeds and measured the deflection on the fin using an electrical sensor,” said Corey Valleroy. “From that we determined the force. Once we have force measurements, we can make predictions of when we need to deploy the fins to reach our optimal altitude.”
Throughout the semester, the team iterated on their design and created a mechanism for the fins to sit securely in an MSP rocket.
The Outcome
By the end of the semester, the team created a workable prototype of their rocket air brake system and delivered it to Mizzou Space Program, which can use the designs and software to develop competition rockets.
“My favorite part of capstone was being able to take all my in-classroom learning and apply it to a real engineering problem,” said Madeline Hartranft. “I enjoyed being able to have a customer, make a product and really see that product completely through its life cycle.”
Discover mechanical engineering at Mizzou!