December 19, 2024
At Mizzou, we believe in the power of hands-on learning. We call it the Missouri Method, and it is an important part of our curriculum and what makes Mizzou Made engineers valuable in the workforce. For Mizzou Engineers, that process culminates with a senior capstone class where students develop solutions to real-world problems.
Students studying mechanical engineering work to engineer solutions to everyday problems. One group of students, Connor Biggs, Caden Cooley, Ryan Deloney, Kathryn Eberhart, Cameron Epperson and Cooper Hinkle, developed a medicine dispenser for people with fine motor disabilities. Their goal was to create a project with a real-world application.
Learn more about the project, how the students worked to develop their product and what they learned from the experience.
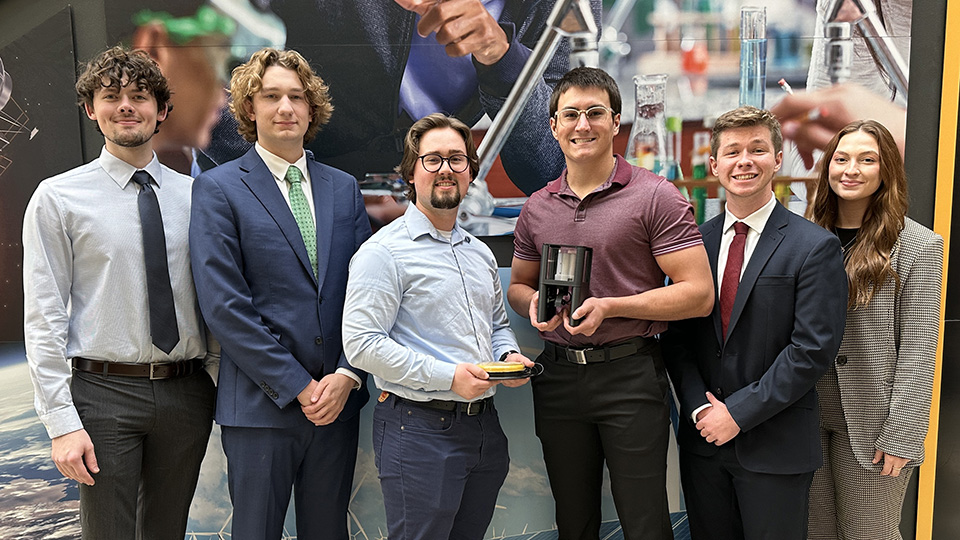
Engineering new solutions to common problems
Caden Cooley: Whenever you take your medication, it can be a huge pain to have to open each bottle. Some people take upwards of five to eight medications a day. So we wanted to try to come up with a streamlined process to combine all of those medications into one device, preloaded, that would allow you to distribute it as needed on a daily basis for as many medications as you need.
Connor Biggs: After we initially met to discuss the project, I mentioned the idea to my girlfriend, who is studying physical therapy, and she suggested making the medicine dispenser specifically for people with motor disabilities. We reached out to other people that were not engineers, to get an outside perspective, and they also thought it was a good idea.
We also talked to the Occupational Therapy (OT) Department, and the main thing that we learned was we wanted to give people more control over their daily lives. That was our guiding principle, giving them more control in something they do every day.
Iterating to find the perfect design
Ryan Deloney: We went through a lot of iterative designs, which we developed using a 3D printer, and worked in teams to design the electronics, devise housing and mechanism, as well as work on our reports and budget. We tested the design with Tic Tacs to determine what needed to be tweaked in the mechanism. Then we would go back to our CAD software and create a new design, a new prototype, a new iteration. We have a pretty big box of scrap prints from that process, but that’s, that’s how we’ve ended up with our final design.
Cameron Epperson: There are some things you can’t foresee or anticipate without actually making the thing. Having it in front of you and trying to put it together the way that you imagine it would go together.
Deloney: Exactly, for example, in CAD SolidWorks, it looks like your prototype will fit together perfectly, you have this big assembly of, like, eight, nine, 10, pieces. Then you actually print it, and things don’t fit or don’t work the way they’re supposed to. The housing went through two or three redesigns, the mechanism probably went through four or five before we reached our final design.
Cooper Hinkle: We only had a semester, less than 15 weeks, from idea creation to developing a working prototype and presentation. Our project had a lot of components, and we did a good job of delegating tasks and bringing everything back together toward our common goal. Our prototype, despite not including everything we fully imagined, was successful, especially given our timeframe. This type of project gives you a taste of the real world, seeing how things come together after multiple teams contribute to how they function.
Epperson: We spoke to many people outside of our normal circle. The biomedical engineer in the occupational therapy department we spoke with was so helpful, and that put us in the right start. We incorporated a lot of what he talked about into our final prototype. I also reached out to pharmacists to get pill dimensions for testing.
Practicing the design process
Kathryn Eberhart: Our coursework over the past four years has given us a strong understanding of how to apply engineering principles to the design process. Group projects and reports in other classes have taught how to effectively manage tasks and break down complex problems under important deadlines.
Additionally, being involved in Mizzou Engineering student organizations and leadership roles, I’ve learned how to navigate group dynamics, work with different personalities, and leverage everyone’s strengths to achieve a common goal.
Cooley: Through this project, we learned the importance of being open to learning and understanding new concepts and going out of your way to try to figure out for yourself. The electrical part of the project, even though none of us are electrical engineers, is a really good example of that, as well as some computer science because we had to code some pieces.
Deloney: Above all else, Mizzou Engineering taught me how to critically think and how to better approach a problem. People who are successful in engineering have a certain mindset, it’s something you have to build, and it takes a lot of time. I believe it’s a product of the work we’ve put into our classes.
Learn more about mechanical engineering at Mizzou!
Read about other capstone projects here.