May 20, 2024
Students studying industrial engineering work with a client to develop solutions to engineering problems. Scroll to learn more about the hands-on projects that students completed this semester.
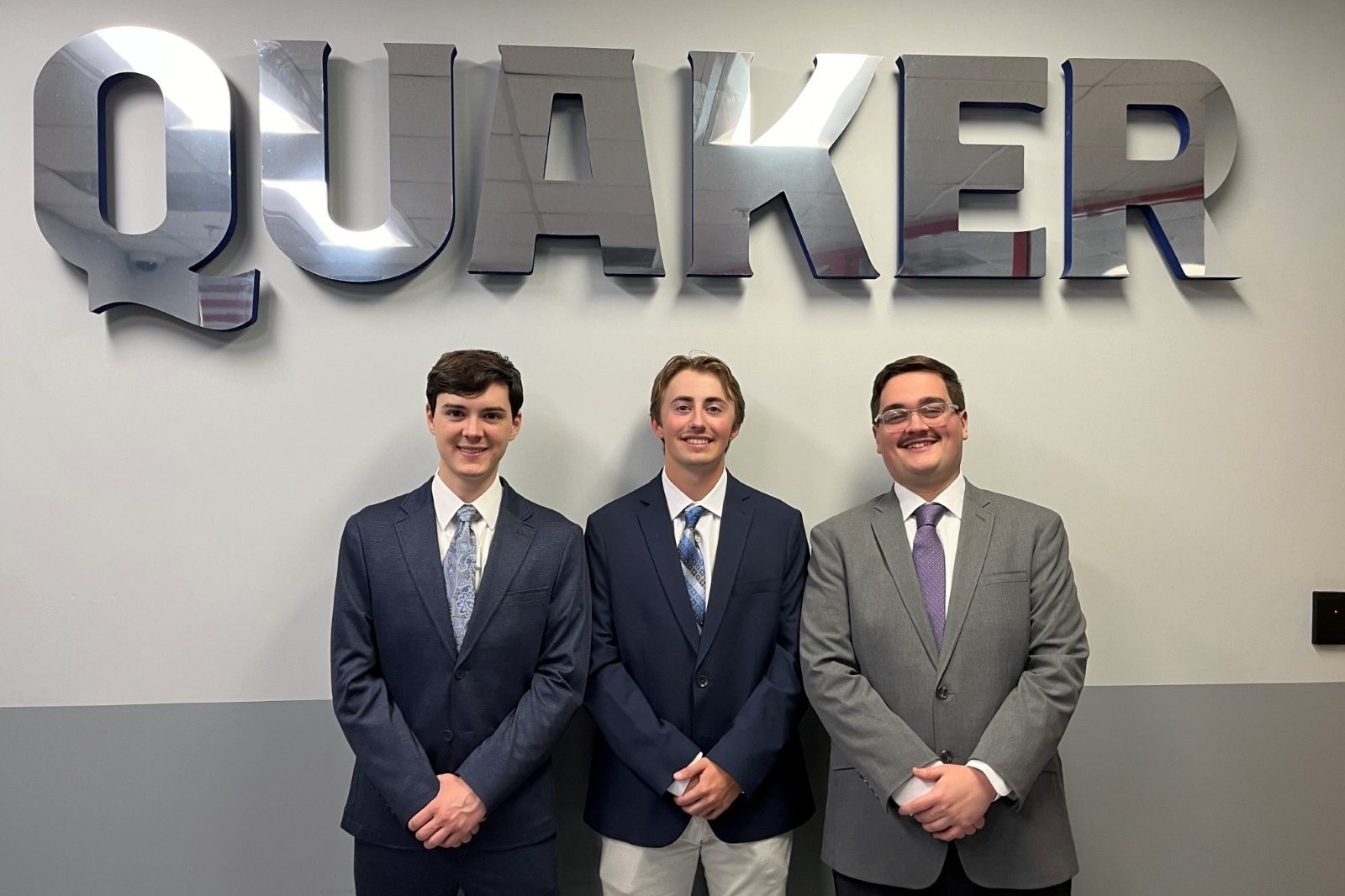
Quaker Oats Popped Rice Crisps packaging waste reduction
Chadwick Bettale, Korben Bruno, Nathan Mashburn
Quaker Columbia is facing issues with product waste due to old sensors being used in the packaging process. PepsiCo, the parent company, intends to replace these sensors but needs more data to justify the expense because operations will need to pause to install new sensors. This capstone group found that the return on investment of new sensors would be achieved in less than two years.
Robinson & Ries Orthodontics
Luke Simon, Profitt Blackburn, Eli Bramblett
Robinson & Ries faces operational challenges in receiving calls, inventory management and the treatment area of their clinic. This capstone group explored ways to reduce missed patient calls, decrease hold times and reduce variation in procedure times. They also created a new inventory management system.
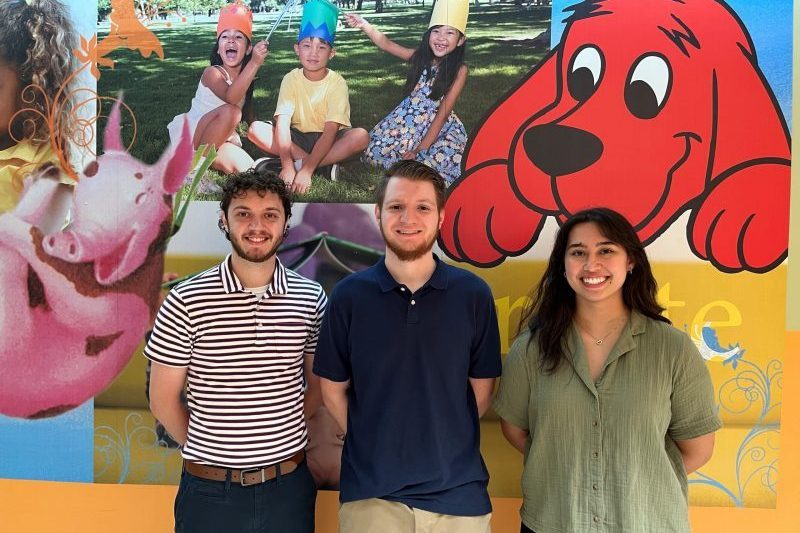
Streamlining packaging’s job setup processes at Scholastic
Natalie Barber, Nick Hummert, Matthew Reynolds
Scholastic’s packaging department produces a variety of products, ranging from shrink-wrapped books to book fair displays. This capstone group worked on improving job setup for workers in the department, with the goals of reducing the composite lifting index (CLI) to less than one, finding opportunities for buffer increases and increasing the capacity of upstream processes by 5%.
Increasing patient throughput at the University Hospital
Josh Burns, Jude Dierker, Shawn Hendershot
MU Health Care has a limited availability of beds, which leads to patient flow bottlenecks. This capstone group explored how to enhance patient throughput and bed utilization by looking at either increasing the number of beds available or by optimizing the patient discharge process.
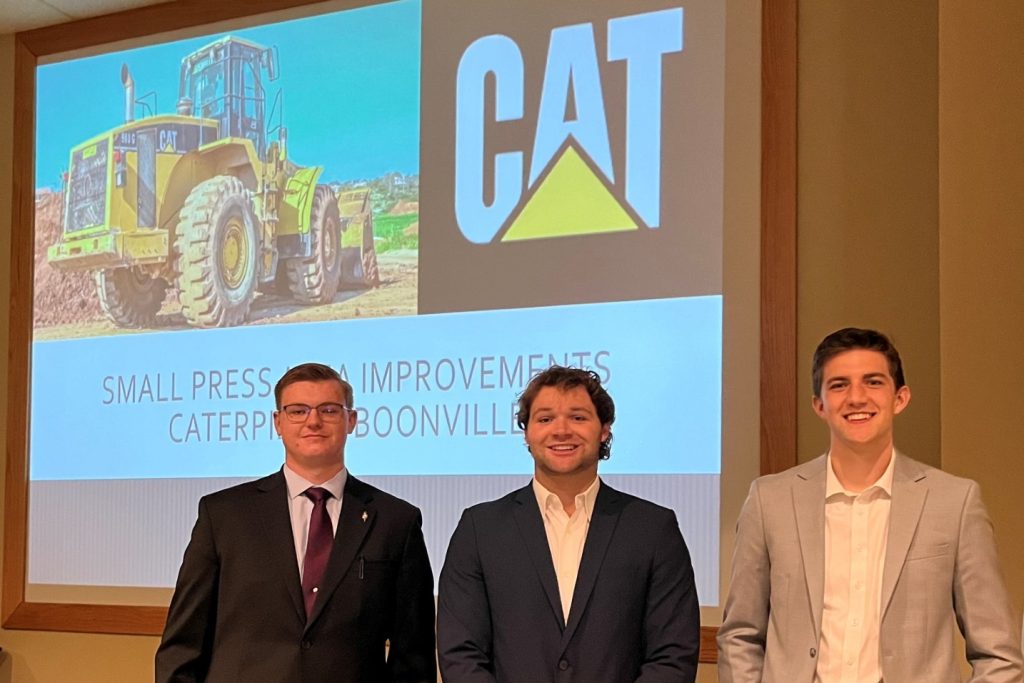
Small press area improvements at Caterpillar Boonville
Adam Heskett, Connor Larkin, Will Norris
Caterpillar Boonville produces parts for the manufacturing of large-scale equipment. The small press area produces over 30 different parts and had concerns about quality control and layout safety. This capstone project investigated improvements to the operational functionality of the small press area at Caterpillar Boonville.
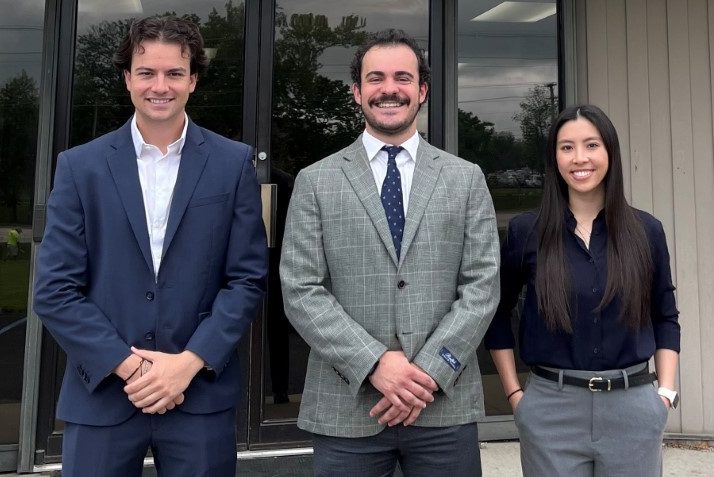
Implementing automation to reduce waste and relieve ergonomic stress at Environmental Dynamics International
Michael Davidson, Jim Vespa, Kim Le,
Environmental Dynamics International (EDI) is constantly looking for ways to improve its operations. This capstone group analyzed their processes to identify potential inefficiencies and determined the best solution would be to implement automation at the flex plug station to relieve the workers of ergonomic stress, increase production and reduce waste.
Learn more about industrial engineering at Mizzou!
Read about other capstone projects here.