November 28, 2022
A Mizzou Engineering team has developed a new technique to fabricate electronics onto everyday objects.
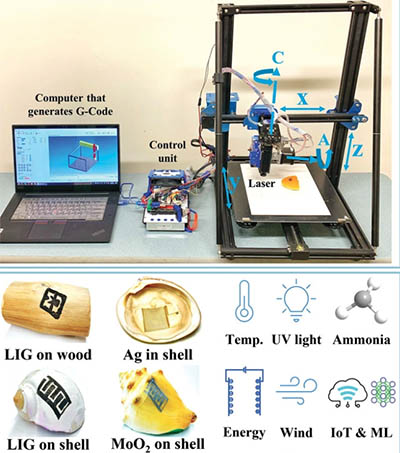
Essentially, the method allows sensors and electrodes to become part of another structure. Without disturbing their own properties, trees could be equipped to measure wind speeds; shells could record water flow; and rocks could detect harmful gases.
“We’re developing a process by which different materials, including those with irregular surfaces, could be made into sensing applications,” said Jian Lin, associate professor of mechanical and aerospace engineering. “The advantage is that these sensors are part of a surface and part of a structure. It opens a lot of routes to manufacturing multifunctional structures and materials.”
Lin developed the laser induce graphene production process as a post-doctoral fellow at Rice University in 2014. That process creates patterned sheets of laser induced graphene (LIG) — a carbon material — from polymers by burning it with lasers equipped in a 3-axis machine.
“Dr. Lin was the first to describe a process of using lasers to convert raw materials into graphene,” said Bujinda Zheng, a PhD student and the first author of the study. “We’ve extended his research from 3-axis to a 5-axis system, shooting lasers onto a variety of curvilinear surfaces to transform material from one state to another. After the transformation, these materials become conductors.”
The novelty of the current work is that the 5-axis laser processing platform to directly fabricate 3D conformable electronics on targeted surfaces with arbitrary surface topologies. Adding two more rotational axes allows engineers to make patterns from all possible directions, increasing precision and the number of possible surfaces to turn into electronics.
With the original 3-axis machine, researchers could make flat, smooth objects like tables or notebooks into electronic devices. A 5-axis machine opens possibilities for more objects, even those in nature, to become multifunctional structures with integrated sensors.
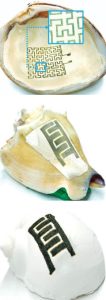
In a paper published in Advanced Functional Materials, the team demonstrated this novel technique to fashion functional devices on clam shells, bread and wood surfaces.
“The advantage of this technique is that we can extend our material library to inorganic materials and apply it to both smooth and rough surfaces,” said Yunchao “Sheldon” Xie, co-author of the work and a research scientist. “We also developed a solution that could be easily applied for further study.”
In the work, they demonstrate the applications of this process in fabricating functional devices directly on the wood, bread, rock, shell, and tree for gas sensing, temperature measurement, UV light sensing, printed circuit board, energy storage, and wind speed sensing. It has potential to create new opportunities in robotics, biomedical sensing, structural health, environmental monitoring, and Internet of Things.
“This technique will take us beyond conventional planar electronics,” Lin said. “It really opens the door to new types of technologies. I am excited to continue to explore the possibilities.”
Other authors include Ph.D. student Ganggang Zhao and Prof. Zheng Yan from the Department of Biomedical, Biological and Chemical Engineering. The work was funded by U.S. National Science Foundation and U.S. Department of The Interior.
Be part of leading-edge research that changes the world. Apply to Mizzou Engineering today!