October 12, 2022
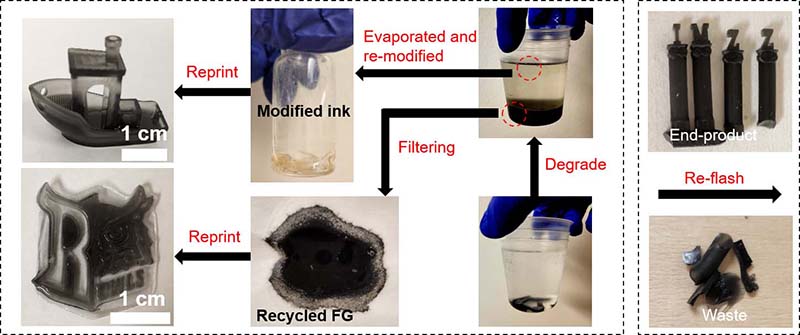
From custom car parts to medical equipment, vat-photopolymerization (VPP) based 3D printing is expected to usher in a new age of manufacturing. Before it becomes interwoven in our daily lives, however, a Mizzou Engineering team is investigating how to make the process more sustainable.
“VPP based 3D printing has a lot of advantages over traditional manufacturing,” said Jian Lin, an associate professor of mechanical and aerospace engineering. “It has advantages of fast rapid prototyping, customized design and localized manufacturing. Still, it has some problems, for example, it’s not as sustainable as it could be.”
The sustainability of VPP based 3D printing is mainly reflected in four aspects (1) minimizing waste generation during printing; (2) deploying renewable raw inks; (3) reuse and recycling printed products; and (4) developing sustainable applications.
To achieve these, Lin and Yuchao Wu — a PhD student in mechanical and aerospace engineering — took a three-pronged approach. First, they developed a renewable printer ink. Second, they developed a way to recycle any materials wasted from the 3D printing process. And third, they outlined ways to apply 3D printing products to sustainable applications.
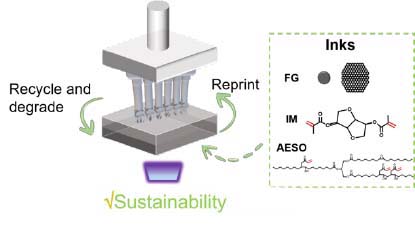
For the ink, the team converted biomass resources from plants into applicable, renewable printing ink.
“The reason we don’t always use raw biomass resources as printing ink is that It isn’t photoactive” Wu said. “Additionally, the properties of products from raw biomass resources usually would not meet industry requirements.”
Therefore, a collaborative research group led by James M. Tour from Rice University refined the wasted material using a flash Joule heating (FJH) to produce flash graphene, which can enhance the mechanical property and absorb the UV light to enhance ink printability.
Moreover, combing FJH with 3D printing makes the printed materials recyclable. That means unwanted materials from printing errors and final products could be turned back into flash graphene.
“We know when we print, there will be wasted materials,” Wu said. “Printing will fail. Even when we get an object we want, it can break. We found a process to reuse excess and broken material.”
Finally, Lin and his team demonstrated ways to use 3D printed materials to make them more sustainable. Specifically, they showed material-saving characteristic in load-bearing applications and printed microfluidic reactors that improve the efficiency of nanoparticle synthesis to save energy.
“VPP based 3D printing is a very promising technology,” Wu said. “But we know sustainability is important. We want to make sure it does not pollute our environment, destroy ecology or waste resources.”
Lin and Wu published their findings in the American Chemical Society journal ACS Nano. Co-authors were Prof. Oliver Giraldo-Londoño from civil engineering, Yukai Yu, Yunchao Xie, Zhenru Chen and Prof. Guoliang Huang from mechanical and aerospace engineering, and Paul A. Advincula and Professor James M. Tour from Rice University. The work was primarily funded by U.S. Army Corps of Engineers (ERDC).
Help engineer a sustainable future. Learn more about mechanical and aerospace engineering at Mizzou.