May 23, 2023
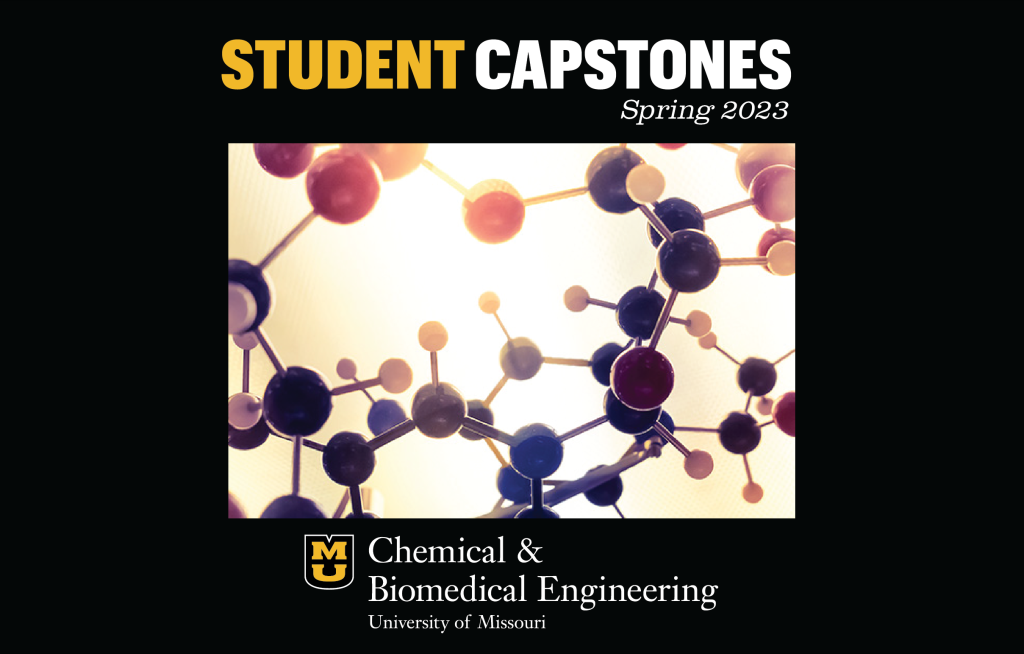
Chemical Engineering students at Mizzou used their capstone project this past semester to create a process to turn recycled plastic into oil for a new material and also provided recommendations to improve recycling practices in Indonesia.
This year, seniors in the capstone class were assigned the 2023 American Institute of Chemical Engineers (AIChE) Student Design Challenge, which asked student to come up with ways to repurpose recycled plastics.
Ahmed Alkhatim, Eric Edson and Hannah Neo made up one group of Mizzou Engineers who completed the design challenge. Read on to hear from the group how they solved the problem and how their education prepared them for the task.
What was the problem your group wanted to solve?
All of the chemical engineering capstone projects this year were solutions to the 2023 AICHE student design challenge title “Closing Critical Gaps in the Circular Plastics Economy.” In summary, it focused on the recycling of plastic waste, collecting it, melting it down into an oil, purifying it, and then processing it into virgin-quality plastic material. The project specifically looked at designing a separation process for the plastic oil to be implemented, as well as making recommendations for improving a recycling sorting facility in Bali, Indonesia. This is a rather important problem that will need to be addressed as the world increases plastic usage. Most of the current plastic waste is either not recycled or is recycled in a way that degrades the plastic into a weaker form (like turning a plastic bottle in to a plastic bag). So having a process that can produce virgin-quality material from recycled waste would increase the interest in recycling and help reduce the plastic waste in the environment.
What were the results?
We designed a separation process that utilized a flashing vessel and fractionating column to separate a 52,000-pound feed of plastic oil into four cuts based on boiling point. Only about 39,000 pounds were usable for the purpose of plastic production; for the rest we gave recommendations for environmentally-safe disposal. We then utilized a filtration system that used alumina and sodium carbonate as adsorbents to remove chlorine and heavy metals from the product streams.
For the sorting facility, we looked at how other countries incentivize their recycling programs and created recommendations for the Bali sorting facility. To generate public awareness and goodwill toward recycling campaigns, a lottery system was recommended to be used to reward households or community members who actively recycle and clean up waste. Rewards could be cash rewards, prizes, discount coupons or tax credit. Additional promotion for recycling should be done through pollution hotspot cleanup events, where locations with large amounts of waste, such as beaches and rives, are cleaned up to show the impact of waste on the local environment, building public awareness and participation. We also recommended that households be given guides on how to recycle and require stricter criteria for recycling; this would mean having separate bags for recyclable plastics and eventually further specifying recycling categories such as requiring sorting by plastic type. This would increase the quality and throughput of the plastic being recycled, which would in turn increase the quality of the oil produced.
For inside the sorting facility, we recommended the use of float filtration, sorting the plastic types by density using brine solutions. Additionally horizontal balers should be used to increase recycling efficiency and reduce downtime, as they would produce larger and more consistent bales of waste at greater volume.
What did you learn during the project?
A lot of this project involved aspects of engineering that we had never looked at before. The chemical engineering department doesn’t focus on petrochemical processes, so understanding fractionating columns and how oils separate was very important to learn. We learned how to contact companies and communicate with them so we could get information about equipment and chemicals. Dr. [Scott] Christensen had us create Gantt charts, a project charter and a work breakdown structure which are all things we had never done before but are useful in industry. It was also a great learning experience to prepare and give a presentation to the Industrial Advisory Board.
How did you Mizzou Engineering education prepare you for the capstone?
Even though there was a lot to learn, this was definitely the culmination of four years at Mizzou’s College of Engineering. The College instilled in us foundational knowledge that we used to solve the project problem, technical skills in using simulation software and writing technical reports, soft skills in communication and time management, and problem-solving capabilities to address the capstone prompt.
Every engineering class we took built our foundation of knowledge and helped us complete our capstone project. From formatting equipment and stream tables, drawing process flow diagrams in AutoCAD, completing economic analyses, and planning chemical safety and control systems. The project thoroughly covered every aspect of course work taught to chemical engineers at Mizzou.
Thanks for sharing!
Learn more about the chemical engineering program at Mizzou and apply today!