November 16, 2023
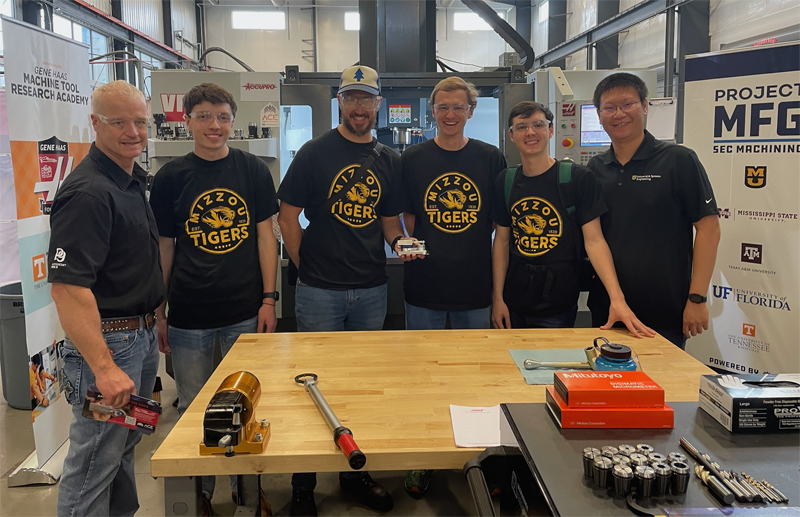
A team of industrial engineering students took third place at a Southeastern Conference competition that challenged them to make an engine that runs off compressed air.
This was the first time Mizzou has participated in the Project MFG SEC Machining Competition, held Nov. 9 at the University of Tennessee, Knoxville.
“We went into this competition as real underdogs,” said team lead Garrett Robison, a Ph.D. student and vice-chair of the Society of Manufacturing Engineers (SME), which helped support the trip. “All of the other teams had done the competition the previous year, had taken a course that teaches how to make the pneumatic engine and had much more general machining experience. We were able to perform as well as we did because of the collective knowledge and training methods of the manufacturing staff here at Mizzou.”
Specifically, participants were tasked with designing a single cylinder pneumatic engine. Groups had to make three components: the piston block, the engine base and the flywheel. At the competition, teams also had to use Computer Aided Design models to create a Computer Aided Manufacturing process and program a machine to cut the parts using a CNC Mill, then assemble the engine.
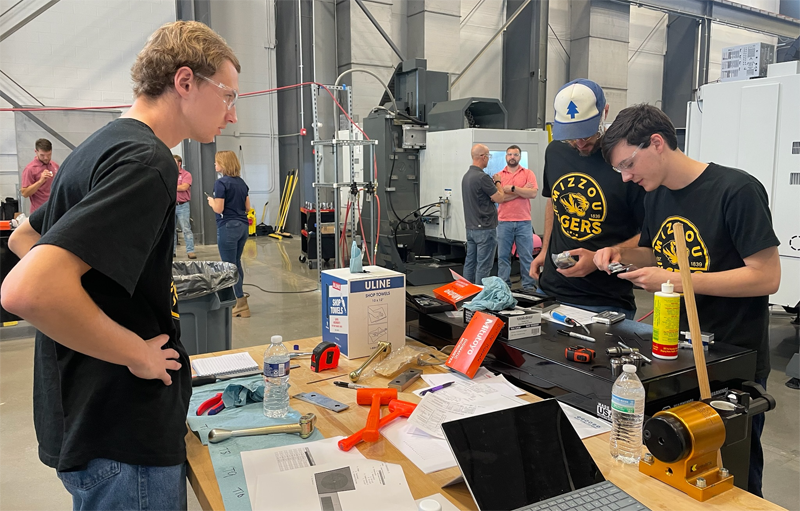
Students prepared for the event for about a month, using similar machinery in Mizzou Engineering’s new manufacturing lab.
“During the leadup to the event, the biggest challenge we had to overcome was a lack of experience,” Robison said. “James West, the manufacturing lab supervisor, was a big help in training us on a CNC machining center.”
The day of the competition, Mizzou’s biggest challenge was accidentally using an incorrect tool. The team realized the error and was able to fix it while cutting the first part, however the mistake cost them about 30 minutes of the four hours they had to complete everything.
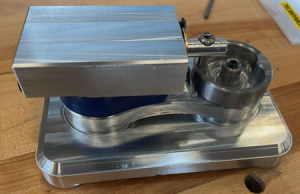
Still, the event was gratifying as it allowed students to implement technical skills and foundational knowledge, Robison said, adding that the group had fun preparing for the competition. It also allowed them to practice using a manufacturing known as 6S—sort, set, shine, standardize and sustain with an emphasis on safety.
“I think we learned a couple of valuable skills,” Robison said. “First, we learned important machining skills such as how to setup operations, how to develop a CAM program and how to run a CNC machine. These are very valuable skills for an engineer to have in manufacturing. Second, we got to implement ideas from industrial engineering, like 6S and standard operating procedures, and see how much of an advantage they gave us in the competition.”
Yi Wang, assistant professor of industrial and systems engineering and expert in manufacturing technology, agreed.
“They started with little knowledge of CNC machines but became masters,” Wang said. “They’ve learned some really practical aspects of manufacturing over the past month.”
The team also included industrial engineering students and SME members Brady Danek, Justin Cypress and Chadwick Bettale.
Master your skills in the industrial and systems engineering department at Mizzou! Apply today.