January 11, 2024
At Mizzou Engineering, we consistently give students ways to pursue discovery with hands-on learning opportunities in their fields of study. That’s why capstone courses are a key pillar of our curriculum, as they allow students to apply concepts they’ve learned in their classes.
This fall, one biological and biomedical engineering capstone group documented their project working with a surgeon to redesign the manufacturing process for a type of medical implant, showcasing another example of how a Mizzou Engineering education prepares students for their careers.
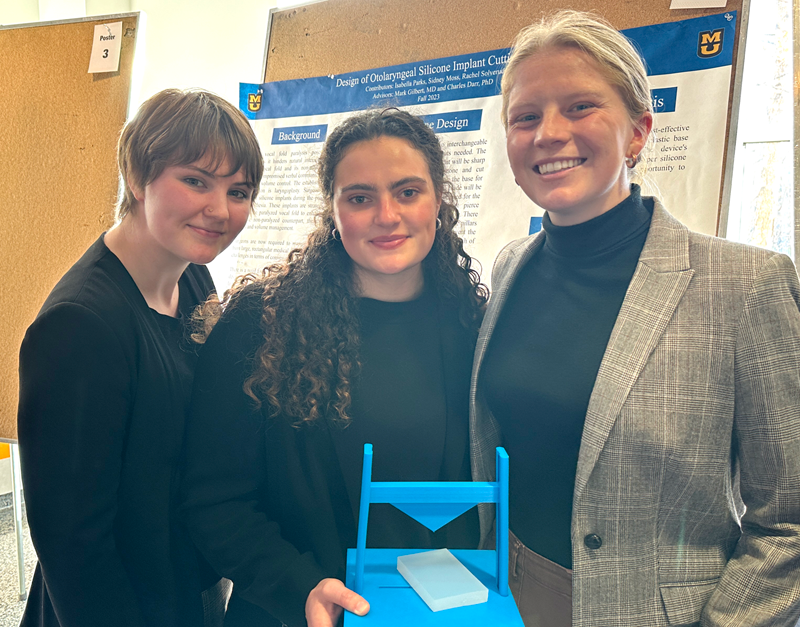
The Project
The capstone team partnered with a surgeon at MU Health who works with patients who have vocal paralysis. The surgeon uses an implant which previously could be carved using a pre-measured piece of silicone, but since the product has been discontinued, he now has to carve by hand while the patient is awake under anesthesia.
“Our goal is to cut down his time,” said Isabella Parks. “I had the opportunity to observe a surgery, and I would say if all things go according to plan, we are saving him 45 minutes during the surgery.”
The Process
The team began by brainstorming the most efficient ways to reduce the time and cost of manufacturing while ensuring safety and product quality.
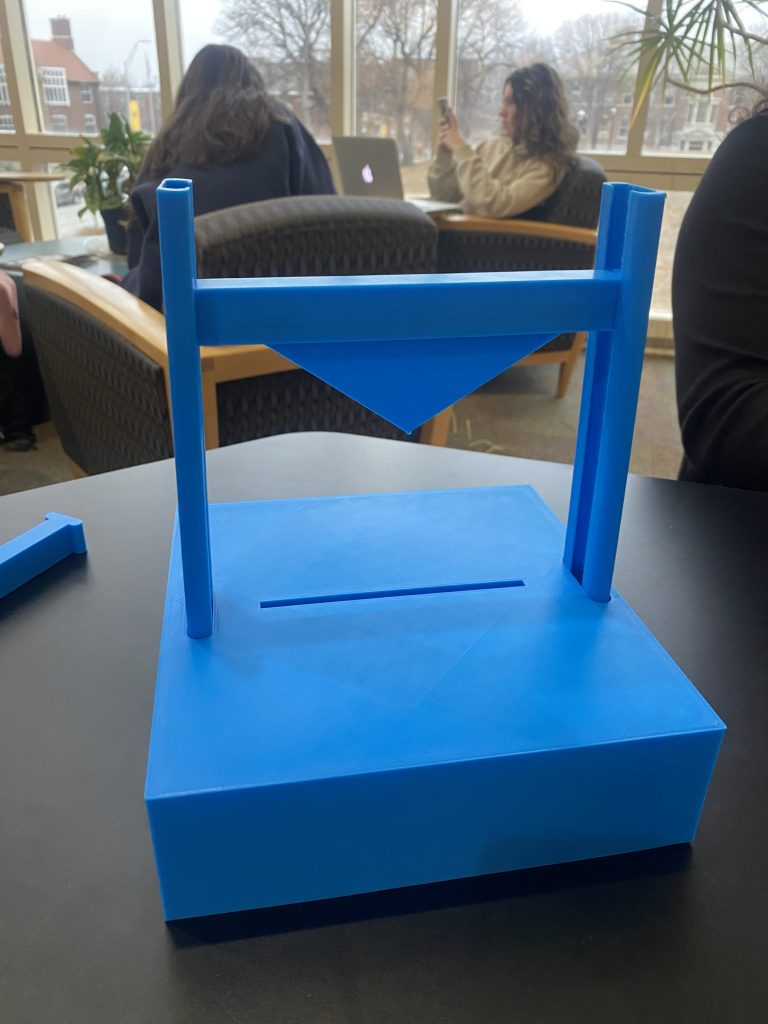
“Essentially, we based our first design off of a typical paper cutter,” said Sidney Moss, “with some significant modifications that enabled us to be more precise and get the angles of cuts that we need.”
After developing the base design, they also added gridlines for more accurate measurements and safeguards to prevent cutting too much off the device. Then, they used the program SolidWorks to create a baseline for the design. The next step was to find a usable blade for the device.
“One problem that we thought about was replacing the blade,” said Rachel Solverud. “It’s going to become dull, and we don’t know if sharpening it will be feasible in a sterile environment. So, we want to move forward with picking a blade and creating the rest of the device around that blade. And from there it will be finalizing our SolidWorks model and ordering parts so we can build a prototype.”
After doing feasibility testing and experimenting with their materials, the group discovered their paper cutter design was less efficient than other solutions. They found that piercing the silicone before cutting worked a lot better than the previous model. The new design is similar to a guillotine bagel cutter, with a sharp point in the middle of the blade that pierces the object before continuing cutting.
The Outcome
By the end of the semester, the team had a prototype of their device and presented their project at the Fall Research Forum in Bond Life Sciences Center.
“The Forum went super well,” said Parks. “We’re really excited about what we accomplished this semester.
Solverud agreed.
“We learned a lot together,” she said. “We completely redesigned our project after it didn’t work out the first time, and that’s an important lesson to learn as an engineer. I’m really proud of all the progress we made this semester.”
Discover biological and biomedical engineering at Mizzou!