January 11, 2024
At Mizzou Engineering, we consistently give students ways to pursue discovery with hands-on learning opportunities in their fields of study. That’s why capstone courses are a key pillar of our curriculum, as they allow students to apply concepts they’ve learned in their classes.
Each semester, chemical engineering students complete the American Institute of Chemical Engineers Student Design Competition. The competition is held in the spring, so students in fall capstone courses solve a prior year’s challenge.
One group of students documented their capstone process, showcasing how a Mizzou Engineering education prepares students for a career in chemical engineering.
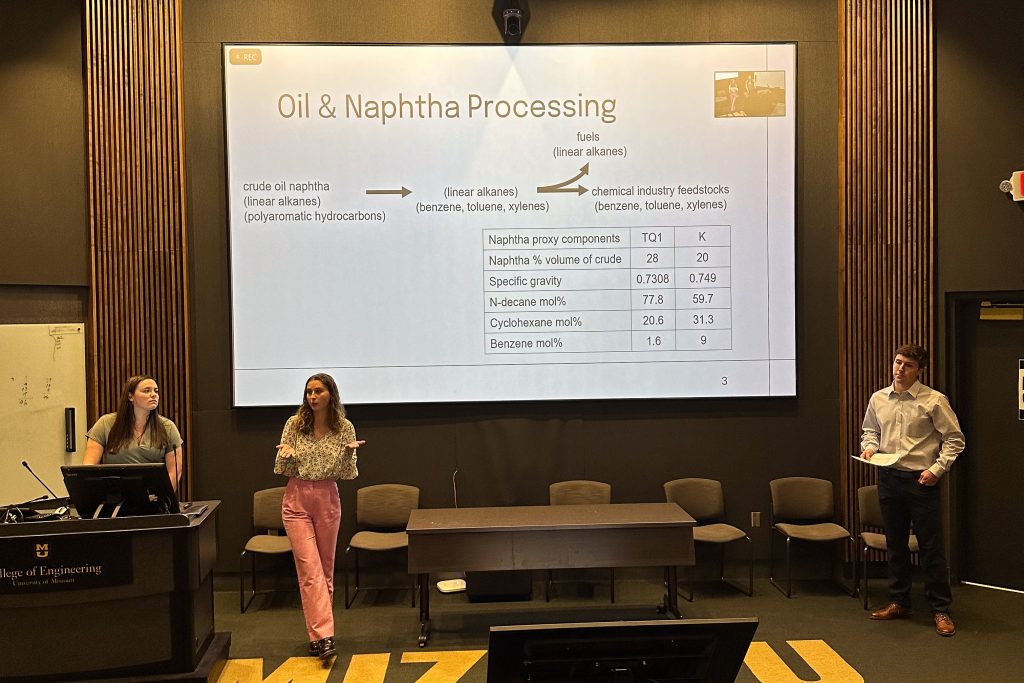
The Project
This fall, students completed a challenge first released for the 2020-2021 academic year, for which they acted as a consulting firm working with a plant in Iraq to retrofit a toppings refinery in order to comply with environmental regulations, so that it can continue to manage imports and exports while turning crude oil into diesel fuel, gasoline and other chemical compounds.
To accomplish the whole prompt, the group divided the project into three parts. Paige Snider would work on creating all the reactions necessary, Kathleen Groner would complete work regarding the extraction of gasoline and Jack Shultz would work on distilling the different chemical compounds benzyne, toluene and xylene.
The Process
The group used ASPEN, a simulation software, to simulate the processes, run them more efficiently and meet all the specifications required by the Iraq plant. As a part of this, they ran sensitivity analyses to optimize the reaction processes and distillation processes.
Finished with the simulation, they began the report by sizing and costing the equipment and ensuring that the materials in the equipment were compatible with the components in the chemical processes before moving onto an economic analysis.
“The economic analysis analyzed how much the plant will be making after 10 years of production,” said Groner. “We looked at it under two different tax regions, 15% and 35%, and in one scenario we’re making roughly $173 million dollars after 10 years.”
Safety was also a goal, and the team looked for ways to simplify the process through minimization and substitution to ensure the plant met safety standards.
The Outcome
In addition to being a great example of a real-world chemical engineering application, the project was a great reminder of the importance of project management in engineering, team members said.
“We also learned the importance of knowing your scope, understanding what the tasks at hand are and making sure that you know what you’re doing so you don’t have to backtrack and redo parts of a project,” said Snider. “Asking questions at the right time is also helpful, so that we know exactly where we should be. And remembering to not be afraid to speak up.”
Shultz agreed.
“If we go on to work at a company, we’ll be assigned our projects like we were assigned this one,” he said. “It was really cool to be able to do this project and be able to apply it to something we’ll do later in our careers.”
Discover chemical engineering at Mizzou!