December 19, 2024
At Mizzou, we believe in the power of hands-on learning. We call it the Missouri Method, and it is an important part of our curriculum and what makes Mizzou Made engineers valuable in the workforce. For Mizzou Engineers, that process culminates with a senior capstone class where students develop solutions to real-world problems.
Each semester, chemical engineering students complete either the current or previous American Institute of Chemical Engineers (AIChE) Student Design Competition challenge. One of the groups, comprised of Becca Bessette, Lilly Orskog, Ethan Simpkins and Reid Wetherington, was tasked with designing a blue hydrogen plant.
Learn more about the problem, how the students worked to solve it and what they learned from the experience.
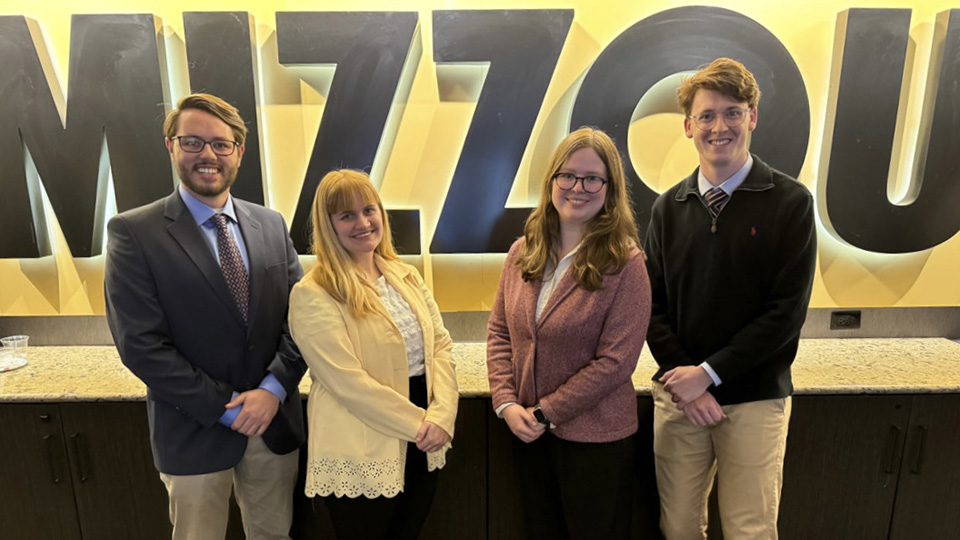
A more sustainable way to produce hydrogen
Ethan Simpkins: We designed a blue hydrogen plant to take advantage of emerging tax credits and to find an intermediate method of producing hydrogen from natural gas that is better for the environment.
Reid Wetherington: We had to have at least 70 percent carbon dioxide (CO2) capture, optimally about 95 percent. We had to produce a certain amount of hydrogen per year, and it had to be on the Gulf Coast.
Lilly Orskog: We additionally had to do a profitability or economic analysis to determine whether or not this project would be viable from an economic standpoint. This included doing a cash flow analysis, as well as researching utility costs and sale prices for our raw materials and our hydrogen.
After we did that, we had to look at the safety aspects of this project: is this project going to be safe to implement into an actual design system? Additionally, we asked what the environmental impact was for all our processes.
An economical solution
Simpkins: We simulated and designed a plant that would produce 250 million standard cubic feet of hydrogen per day. Then, we designed a series of separation techniques that would create a pure hydrogen stream and would separate out carbon dioxide before it’s released into the atmosphere.
Wetherington: When we looked at our profitability, we had the potential to make $1.4 billion in net present value over 15 years.
Simpkins: This project is very relevant because part of this project is deciding whether to utilize tax credits that went into effect in January. And so it’s a very new emerging economic landscape. There are real companies that are evaluating the same project right now. It was cool to have a very relevant project with technology that is still emerging, so there was a lot of variability with how we could design it
Wetherington: I think there are currently some power plants in Texas or Ohio that are using these tax credits to produce energy, so it is actively being researched and used. This was a useful project to understand what the power generation landscape looks like.
Putting it all together
Simpkins: I would say one big thing we learned is how to put all of our classes together. We have all these classes that are really theoretical and very specific to things like heat transfer, mass transfer, thermodynamics, etc., and when you look at them all independently, it’s hard to picture how they come together. Doing a project like this, you have to consider every aspect of that in your process. It forces you to sit down and think, practically, what would this look like? What assumptions can we make? How do we come up with a clever design?
Wetherington: I had to do quite a bit of research on the CO2 separation and other aspects of the project. I was able to dive into learning about the different methods that are available in the industry. And the method we ended up going is very new, and only few pilot plants are using them, it’s not really in the industry yet.
Orskog: One of the most important things I learned is how to utilize the tax credit. We hadn’t worked with those in our previous semester design project or during the economics part of our course. So we spent some time figuring out how we could use it and if there were any limitations that we had to meet or stay under. And a lot of our profit ended up coming from that tax credit.
We have a Design I class before Design II that has been extremely helpful in giving us a strong foundational basis of the culmination of all our classes coming together. We focused a lot last year on the design process itself, learning the heuristics for designing our different pieces of equipment, as well as learning how to do that basic economic analysis to determine whether or not our project will be profitable. Dr. [Scott] Christensen did a wonderful job of bringing everything that we’ve learned over the past four years together to provide a good basis to be successful with our capstone project.
Wetherington: Dr. [Reginald] Rogers, one of our professors, once told us his goal for is to give us a toolbox and to fill it with a bunch of tools that we can use in chemical engineering. He said the greatest tool is our intuition about a project.
Multiple times we had parts of the project not make sense. We knew what it should have been, or approximately what it should have been but the software would provide a strange value. And it sometimes didn’t give an error but we knew that was an error. So that was one of the most helpful things we learned, the intuition that a lot of the classes have just kind of built up over time.
Simpkins: Chemical engineers can do a wide variety of things. Even this project, I never would have guessed that our capstone project would have been hydrogen production. It’s great to practically see how we can apply our knowledge to a wide variety of different processes.
Learn more about chemical engineering at Mizzou!
Read about other capstone projects here.