June 27, 2022
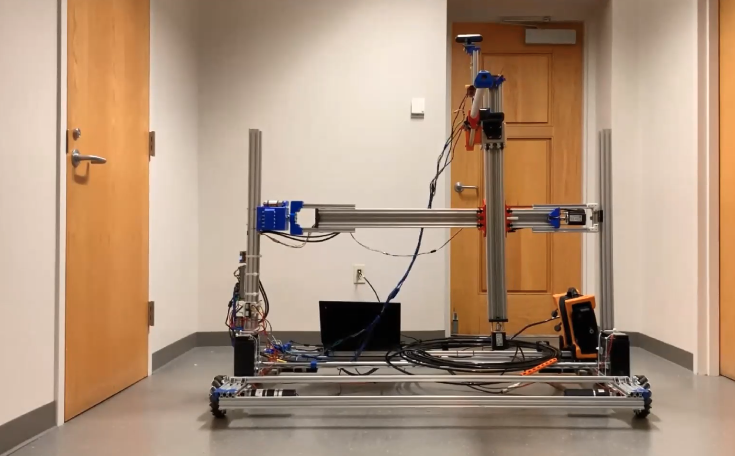
The demand for energy is expected to increase rapidly over the coming decades, and power plants need to run efficiently to keep up. That’s why a Mizzou Engineering team is designing a robot that can automatically inspect heat exchangers, devices that are critical to generating electricity.
Right now, power plants use a technique known as eddy-current testing (ECT) to detect and characterize flaws in some power plant components such as heat exchangers.
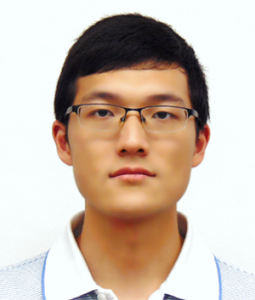
“To keep power plants at high efficiency, you need to maintain the heat exchangers regularly, and that requires human technicians with experience and steady manipulation to operate the ECT inspection device,” said Bujingda Zheng, a PhD student under the supervision of Jian “Javen” Lin, an associate professor of mechanical and aerospace engineering (MAE). “That process is time-consuming and labor-intensive. Our goal is to develop a robotic platform that autonomously do the operation, obtain the data, and then analyze it with a trained machine learning model.”
The robot is on a Mecanum-wheeled chassis, making it mobile, and it uses machine vision to locate tube bundles and inlets inside of the exchangers. The robot can operate the ECT probe to collect information from the exchangers, and the system analyzes the data in real time to alert power plant operators of any problems.
The machine learning component ensures that the robot will become smarter over time. As it collects information from a wider variety of heat exchangers, the computer will build upon its knowledge and learn all the unique ways the devices could be defective.
“We’re training the machine on what to look for in regard to what’s defective and what’s working,” Zheng said. “In order to make the machine more commercially viable in the future, we have to collect information from enough tubes to make our own comprehensive data set.”
In addition to building the data set, researchers are also looking for ways to make the prototype more agile and compact for industrial use.
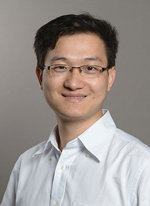
This work was accepted for publication in Journal of Field Robotics. Authors are Bujingda Zheng, Dr. Jheng-Wun Su, Lin’s prior Ph.D. student, currently an assistant professor at Slipper Rock University (PA, USA), Yunchao Xie, Jonathan Miles who was a MAE undergraduate, Hong Wang, Wenxin Gao, MAE Professor Ming Xin, and Lin. Former MU Power Plant director Gregg Coffin offered consulting information for this project. This project was funded by US Department of Energy (Award #: DE-FE0031645) under the management of Dr. Heather A. Hunter at National Energy Technology Laboratory (NETL).
The paper is the first to come out of this project, which is in its third year and one of the reasons why Zheng chose to attend Mizzou Engineering for his PhD.
“I did my bachelor’s and master’s degrees in traditional mechanical engineering, but I’m really interested in robotics,” he said. “Dr. Lin was the only professor who offered me this kind of opportunity. The professors at Mizzou are really open minded and are open to your ideas — and ideas are critical for innovation.”
Be part of an engineering program open to your ideas. Learn more about mechanical and aerospace engineering at Mizzou.